Laser drilling is a process that has revolutionized the manufacturing industry. It is a complex but highly efficient process that allows for the creation of extremely small thru-holes, with a diameter as small as 0.002 inches. The high precision and accuracy of laser drilling have made it a popular choice for various applications, including medical devices, aerospace, automotive, and electronics.
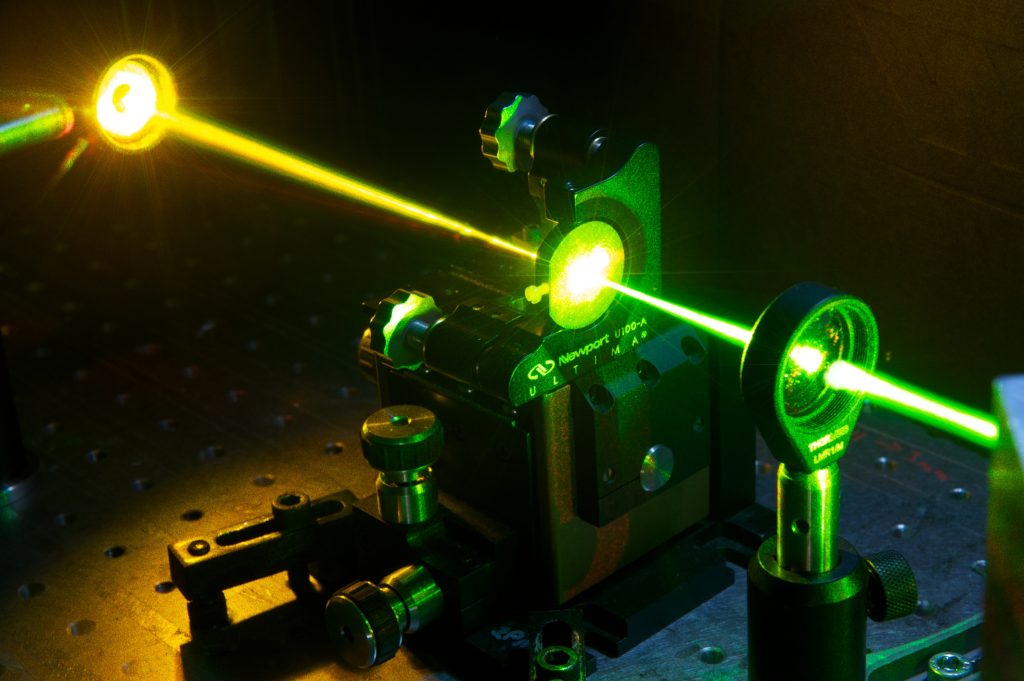
The laser drilling process involves the use of a high-powered laser beam, which is focused onto the surface of the material. The laser beam then pulses rapidly, emitting small bursts of energy onto the material, causing it to melt and vaporize. This creates a small hole or thru-hole in the material. The process is known as percussion drilling.
One of the key advantages of laser drilling is the ability to control the diameter of the thru-hole precisely. If a larger hole is required, the laser is moved around the circumference of the hole until the desired diameter is reached. This technique is called trepanning.
Laser drilling is used in various applications to create thru-holes in a range of materials, including metals, ceramics, plastics, and composites. The process is essential in the aerospace industry, where small thru-holes are needed in critical parts, such as turbine blades and engine components. Laser drilling is also used in the medical field to create thru-holes in stents, catheters, and other medical devices.
The accuracy and precision of laser drilling make it a popular choice for electronics manufacturers, especially for creating thru-holes in printed circuit boards (PCBs). PCBs are vital components in many electronic devices, and their performance depends on the accuracy and precision of the thru-holes that are drilled into them. Laser drilling offers unparalleled accuracy and precision, resulting in PCBs that are reliable, efficient, and durable.
In addition to its high precision, laser drilling also offers several other advantages over traditional drilling methods. For example, laser drilling is a non-contact process, which means that there is no physical contact between the laser and the material, resulting in less wear and tear on the equipment. Laser drilling is also faster than traditional drilling methods, allowing manufacturers to produce more parts in a shorter amount of time.
In conclusion, laser drilling has revolutionized the manufacturing industry by providing a fast, accurate, and precise method of creating thru-holes in a wide range of materials. Its ability to create small diameter holes, its high precision, and its non-contact nature make it an essential tool in many industries, including aerospace, electronics, and medical devices. If you're looking for a reliable and efficient way to create thru-holes, laser drilling is the way to go!