Low-pressure casting (LPC) is a casting process that uses a pressurized furnace to inject molten metal into a die under low pressure. The process is similar to high-pressure die casting, but with some key differences. In LPC, the molten metal is poured into a holding furnace, which is pressurized with an inert gas such as nitrogen. The pressure forces the molten metal up through a riser tube and into the die cavity.
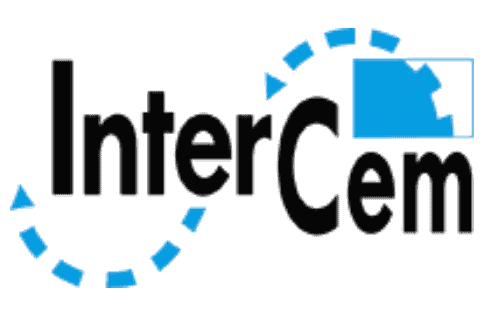
One of the advantages of LPC is its ability to produce high-quality castings with very thin walls and complex geometries. The low pressure ensures that the molten metal flows evenly and uniformly through the die, resulting in a smooth surface finish with minimal porosity. The process is also highly suitable for casting low-to-medium volume parts.
LPC is mainly used for casting aluminum alloys, which are widely used in the automotive, aerospace, and consumer goods industries. The process is also suitable for casting magnesium and zinc alloys. LPDC is an eco-friendly process as it uses less metal and energy than other casting processes. This makes it one of the most cost-effective and sustainable methods of manufacturing metal parts.
The LPC process has several advantages over other casting methods. These include:
1. Low porosity: The low-pressure casting process produces parts with low porosity, eliminating the need for additional processing such as impregnation or welding.
2. High quality: The LPC process produces high-quality castings with uniform thickness and smooth surface finishes.
3. Low scrap rates: The LPC process is highly efficient and produces minimal scrap, making it a cost-effective process for casting complex parts.
4. Computer-controlled: LPC can be easily automated and monitored using computer software, ensuring precise control of the casting process.
In conclusion, low-pressure casting is an excellent option for producing high-quality metal parts with minimal waste. It is a cost-effective and sustainable process that is suitable for casting low-to-medium volume parts. The process is also eco-friendly and can reduce energy consumption and material waste. With its many advantages, it is no wonder that low-pressure casting is becoming increasingly popular in the manufacturing industry.